We are excited to lead the € 2 million seed financing round of Darmstadt-based Energy Robotics alongside a syndicate of experienced angel investors. The exceptional team around the founders Marc Dassler, Dr. Dorian Scholz, Dr. Stefan Kohlbrecher, and Dr. Alberto Romay built a hardware-independent software operating platform for mobile inspection robots that will change industries.
Rigorous inspection prevents catastrophes
March 2012. Uncontrolled gas leaked out on the “Elgin’’ drilling rig in the North Sea. The French operator Total was unable to detect a rusty pipe which eventually led to a billion-dollar damage for the company. And even worse, it led to significant risks for employees and the environment. While Total has learned their lesson and dramatically increased their inspection efforts to detect leaks before they grow and eventually break, it is just one of many examples across industries. Despite the variety of catastrophic scenarios, there is one simple commonality: You do not want heavy, dangerous machines to break.
Today, the importance of proper inspection is not a secret, but unfortunately it conflicts with the constant need to reduce costs. Regrettably, competitive pressure leads companies to trade cost savings for safety either in the form of reduced inspection frequency or inappropriate inspection conditions. Morally, neither one is acceptable. On top of that, several inspection jobs are more or less impossible for humans to perform. As a result, industrial inspection is not done as it should be.
🤖 Robots as a key to enhance safety
Luckily, robots are uniquely equipped to perform dull, dirty, dangerous and dear jobs (aka the 4 Ds of Robotization), and take over repetitive inspection jobs from humans. The increasing commoditization of robotic hardware has continuously decreased costs so that, today, robots can compete or even outperform human labor from a cost perspective. As demand from emerging economies encourages the production of robots to shift to lower-cost regions, they are likely to become cheaper still.”) More importantly, however, robots won’t get sick and provide a constantly high quality of inspection results which ultimately maximizes the level of safety. Aggregating the different interests of a customer, it becomes clear that a safety-(which includes the quality and robustness of the required signal/information, as well as the safety for humans and environment),-to-cost ratio is the most suitable perspective to evaluate different solutions.
To better understand the requirements for inspection solutions, we spoke to a variety of industrial companies. On the most basic level, all companies tend to distinguish their use cases based on the impact of a hypothetical worst case scenario. Scenarios range from machine damage as the mildest impact over environmental damage as an intermediate one to human damage as the worst impact. What might be worse than human damage? Well, human damage together with environmental and machine damage. Ironically, the search for such black swan scenarios leads us back to the oil & gas industry where humans use heavy machines to flow oil. Not too different, Energy and chemicals provide similar potential for a catastrophe. One thing is certain: compromising on safety in such industries would be more dangerous than for other industries, take for example production companies (like a cookie factory.)
💹 The market opportunity
Diving one level deeper, the requirements within an industry can be dissected along two dimensions: 1. external conditions and 2. information to be collected. Sticking to the oil & gas industry, it can be split into upstream, midstream and downstream companies.
- Across these groups, we find a variety of site types such as drilling facilities, reservoirs, gathering facilities, separation plants, pressure boosting facilities but also refineries. All of them provide different risks and face completely different external conditions. Some of them are on ground level, some of them are multi level and connected with stairs. While some face humid conditions offshore in the sea, others are onshore and exposed to extreme heat. The list goes on.
- In addition to a variety of diverse conditions, the use cases themselves differ a lot based on the information of interest. Sometimes companies need to control pressure and another time they need to sniff for gas. While in some use cases rust is a threat for safety, in other use cases it’s a broken weld seam. Similarly, the list goes on.
The combination of different external conditions plus the information of interest defines the requirements for the robot hardware platform (wheels, chains, 2 legs, 4 legs, etc.) and the type of sensors (LiDAR, camera, gas detectors, etc. — which in turn add further requirements regarding the payload of the hardware platform.) Mapping the most obvious inspection use cases and calculating the addressable market size based on the jobs that can be performed by robots already today, a bottom up analysis for oil & gas, chemicals and energy leads to a potential of $ 10–12 billion.
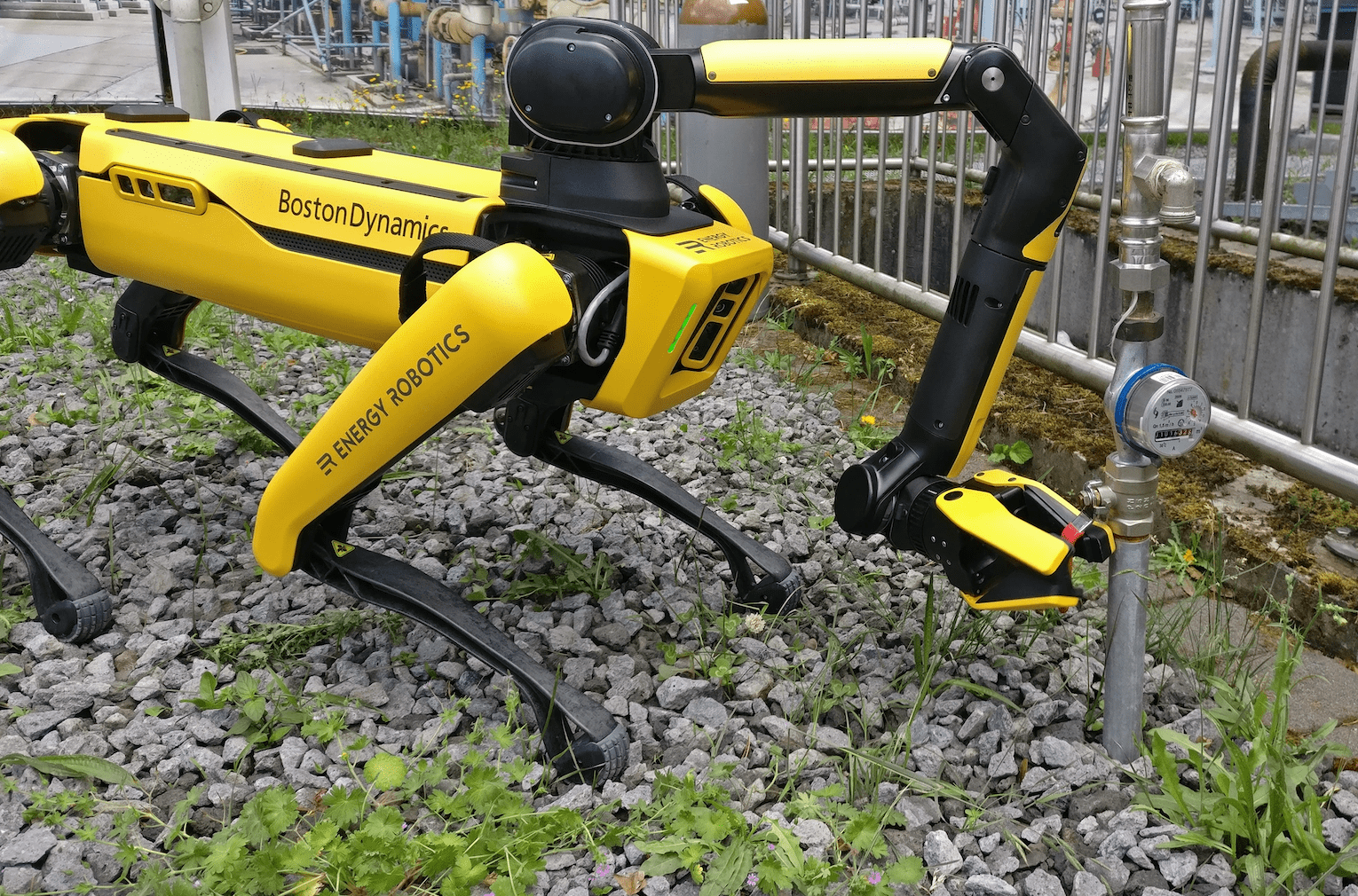
While these use cases are all about information collection via sensors, Boston Dynamics recently added an actuator arm and thereby entered the world of manipulation. With continuously increasing capabilities of robots and an increasing willingness to use such innovative solutions on the customer side, the variety of use-cases is exponentially growing and I’m afraid that today we cannot even gauge the full potential of mobile robots within industrial contexts. Interestingly, the growing diversity of use-cases leads to an important conclusion: the more diverse these use-cases become, the more diverse the requirements will be for the respective robots.
👩🏼👨🏾👵🏼 Diversity matters
Sure, Boston Dynamic’s human-like Atlas would probably be able to perform most of the tasks. But would you be able or willing to pay a few hundred thousand dollars to know the pressure of your pipe if a remote-car-like robot with a camera would be able to provide the same information for less than 10k? Said differently, if you’re looking for a tool to open a bottle of wine, would you buy a Swiss Army knife for 100 bucks or a corkscrew for 5? Yes, the corkscrew does the job (probably even better) for only a fraction of the cost. Sticking to this analogy, every tool of the Swiss Army Knife represents another human skill. While the corkscrew might have the ability to walk on flat ground, the saw might have the ability to climb stairs, or the tongs might demonstrate waterproof-readiness.
When looking into the variety of suppliers, it becomes clear that in line with the analogy above, there is a continuum ranging from specialists such as ExRobotics or Rover Robotics that can perform few tasks specifically well, and generalists that can perform a variety of tasks at an acceptable (or even exceptional) level, such as Anybotics or Boston Dynamics. Zooming into the offerings of the tens of suppliers on the market, we find that few of them offer more than three or four robots. More interestingly, robots across the portfolio frequently follow a company-wide strategy which is either generalist or specialist within a specific industry or skill dimension.
For example, Boston Dynamics offers the walking dog Spot and the human-like Atlas (they discontinued several other projects.) Two robots which are both generalist solutions that can perform a great variety of tasks to an acceptable (Spot) or exceptional (Atlas) level. Similarly, Anybotics offers ANYmal C, a generalist solution similar to Spot. As another example, ExRobotics offers four versions of a crawler based robot, all of them specialists with a crawler-based approach for rough, hazardous areas. The list goes on and it shows that no matter the size of the portfolios, all robots within it tend to follow the same company wide strategy: generalist versus specialist.
Taking the safety-to-cost ratio perspective and applying it to the variety of use cases with a diversity of requirements, it becomes clear that for every use case there is likely another specialist solution with the optimal ratio. As specialist robots are oftentimes simpler than their generalist pendants, they tend to be cheaper too. Few cases require a generalist robot that is able to perform a variety of tasks on a human-like level. As a result, I expect that the incentive to optimize safety while reducing costs will gradually drive customers to more specialized robots.
🤝 Controlling diversity requires a common basis
Speaking to a range of customers who are keen to use robots for industrial inspection, we noticed that they tend to start with one use case as a pilot. Once it is successfully proven, they either roll it out across the firm or they immediately approach the next use case. Being forced into more specialized solutions, they will likely find themselves with a different robot supplier than in the first use case. This is the point where the frustration begins.
Most robot suppliers are full-stack providers that assemble hardware (including actuators and sensors) and software. Although the Robot Operating System (ROS) is a wide-spread approach to standardize control softwares, the software interfaces from the different suppliers are as diverse as the use cases. As a result, working with two or more robot suppliers directly is like working with Windows, Android, iOS and Linux at the same time. Nobody would even think about doing this today. Clear the stage for Energy Robotics!
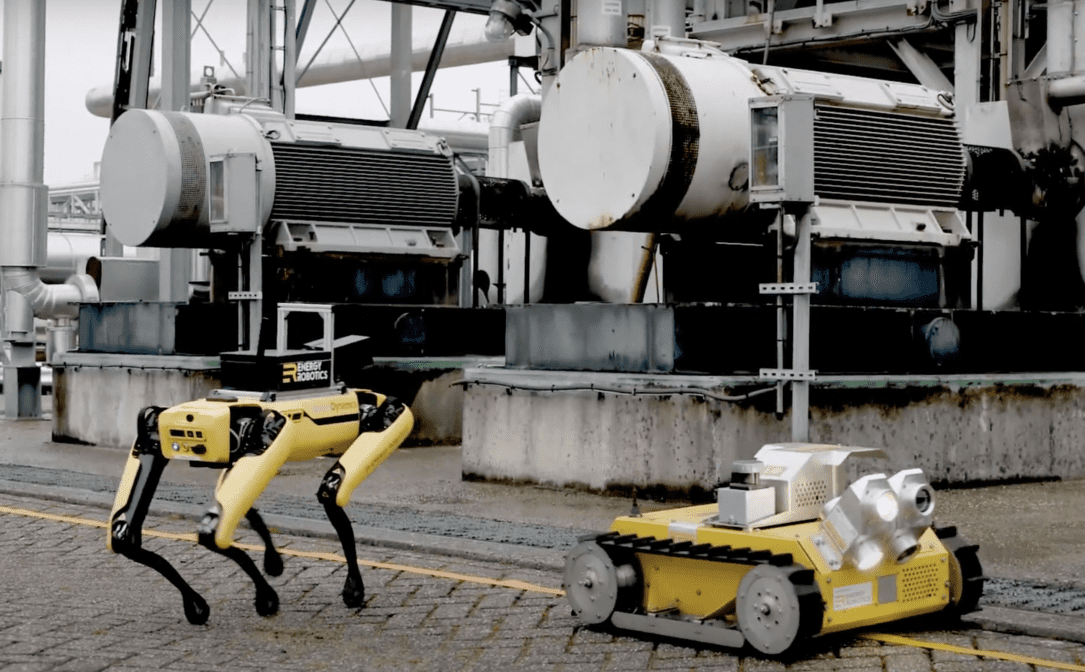
Hardware-independent software platform
Extrapolating recent trends into the future, we’re firmly convinced that mobile robots will become increasingly specialized (and commoditized) in the midterm; this requires a hardware-independent software operating system for mobile robots. And this is exactly what Energy Robotics does. With more than 15 years of robotics research at TU Darmstadt and numerous awards under their belt, such as the RoboCup World Championship (won multiple disciplines across several years, last in 2019) or the WRS Plant Disaster Challenge (2018), the team around Professor Dr. Oskar von Stryk has learned to adapt their software to control more than 20 different hardware platforms over the years. By creating several abstraction layers and more than 200 independent software building blocks that run smoothly together like a gear wheel, the team was able to reduce the time to control any new hardware platform through their existing software within weeks.
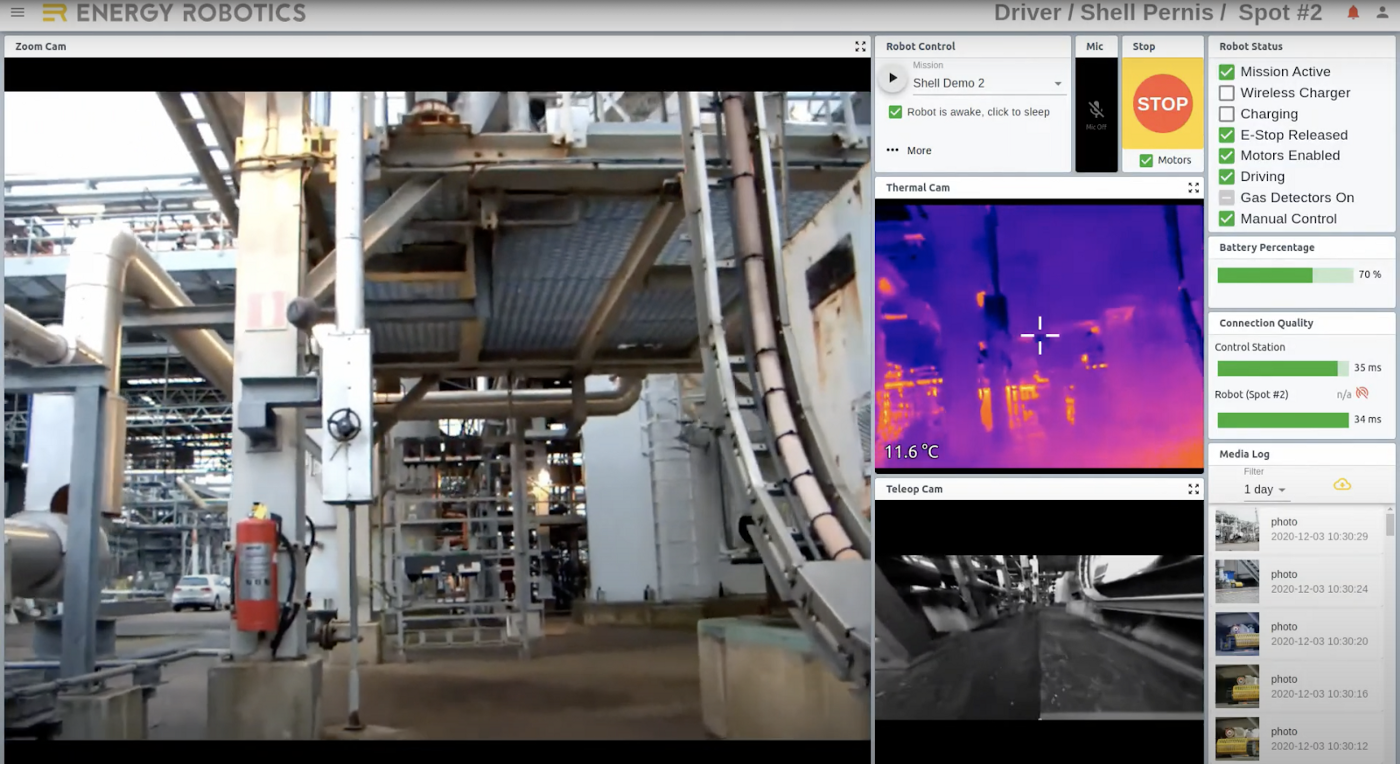
Circling back to the oil rig catastrophe, Total has learned their lesson and started to prioritize inspection and safety more than ever before. As part of these efforts, they launched the famous ARGOS challenge (Autonomous Robots for Gas and Oil Sites = ARGOS) which Energy Robotics won as the first team in 2017. As a result, Oskar together with his Postdocs Dr. Dorian Scholz, Dr. Stefan Kohlbrecher and Dr. Alberto Romay, spun out Energy Robotics. They got in touch with their long-lasting friend and previous colleague Marc Dassler, (who conducted research on walking robots with Oskar in 2004) to productize their world-class research and start building a proper company in 2019. Less than two years after founding the company, their solution brings together a hardware-independent robot operating system, cloud-based fleet management, and AI-driven data analysis for industrial applications.
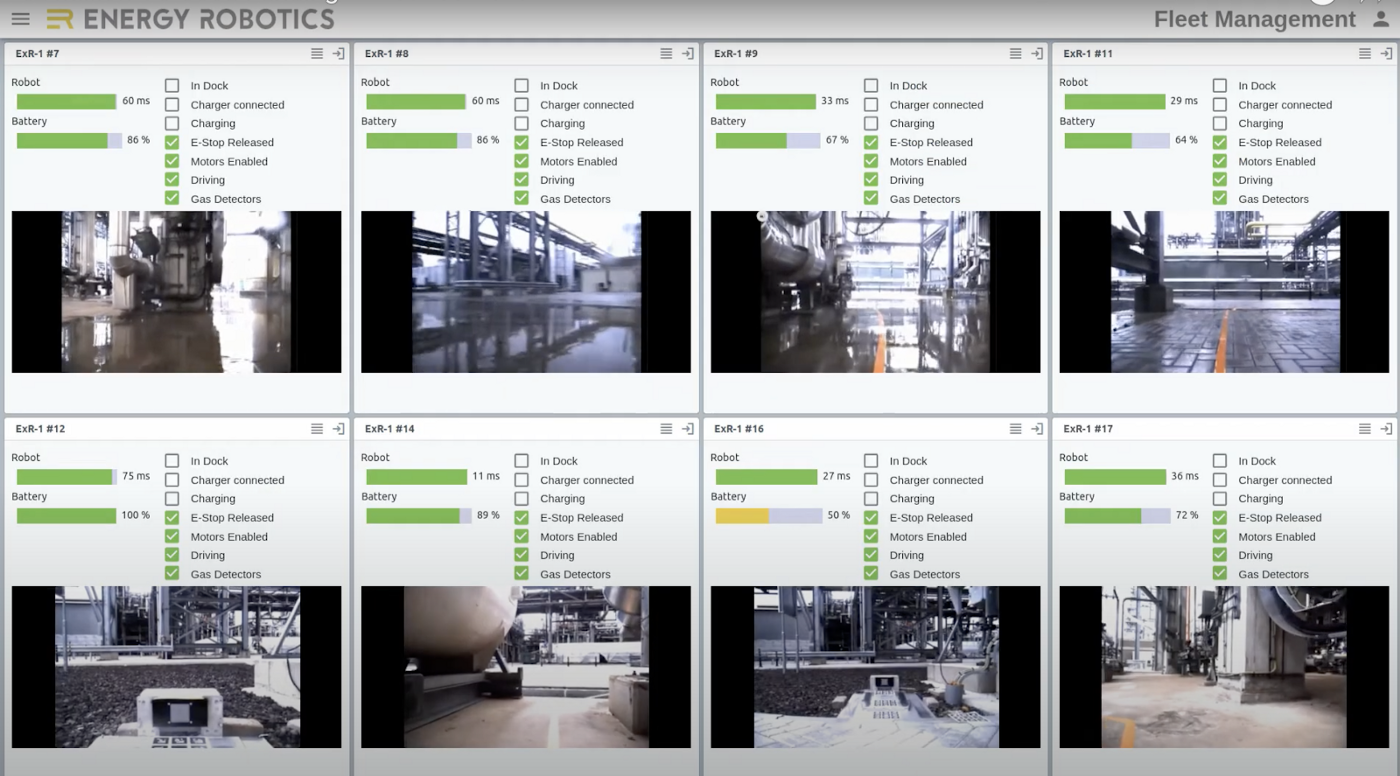
With specific applications resulting from the ARGOS challenge and a unique software solution at hand, the team has started to partner with selected hardware suppliers such as ExRobotics, and quickly won their first customers within the oil & gas sector. With their first successful pilots, interest has started to spread and customers with similar use cases in adjacent industries like chemicals, pharma and energy got in touch. In the meantime, Energy Robotics has equipped more than 20 robots in operations across 4 continents that performed more than a total of 20.000 hours of inspection. To serve an increasing number of customers, explore new use cases and advance the product, the team has decided to take the next step and raise a seed financing round.
We are happy to announce that together with an exceptional angel syndicate including multi-advisory board member Dr. Paul Achleitner, ex CEO OMV (oil & gas tycoon with $25bn+ in revenue) Dr. Gerhard Roiss, CEO and founder of has-to-be Martin Klässner and well-known angel investor Andrej Henkler, Earlybird led the € 2 million Seed financing round of Energy Robotics.
Team Energy Robotics, welcome to the #EBVCgang! We’re excited about the journey ahead.
Dr. Andre Retterath is a Principal at Earlybird Venture Capital. He holds a Phd from TU Munich.